
October-November 2022
Looking Back...
Looking Forward
------------------
|
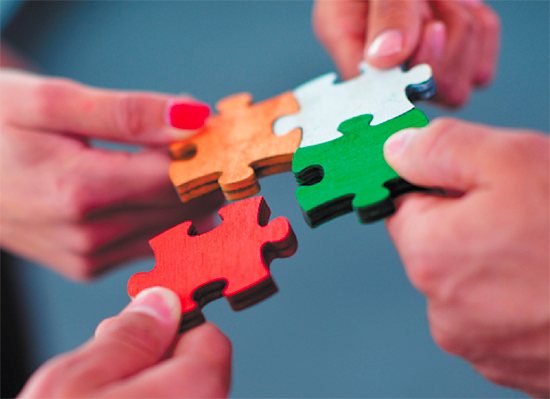

BROWN ON GREEN | Supply Chain
The way manufacturing companies do business has changed through the years. In the past, a manufacturer produced massive amounts of product and warehoused the inventory until orders required restocking. This meant factories boomed when inventory was low with short-term layoffs during times of less demand.
This all changed in recent years when manufacturers discovered the “just in time” method of production. Less inventory cut the cost of storing massive amounts of product. The productivity of businesses skyrocketed because this greatly reduced overhead costs and the costs of shutting down and restarting the factories. It also was better for workers because it reduced short-term layoffs. Soon, nearly every business adopted the “just in time” method of making their products.
In 2020, when the pandemic hit, it completely disrupted the “just in time” process of manufacturing goods. It even affected service industries because personnel were deployed to be “just in times” when needed. During the pandemic, personnel recovering from COVID, along with surges in demand for certain goods, caused shortages, because “just in time” manufacturing could not keep up with demand.
For instance, we all remember the shortage of toilet paper when the U.S. population panicked and began hoarding it. Factories had been finely tuned to manufacture just enough—but not too much—toilet paper to avoid storing it in warehouses. Meat-packing plants slowed production and some plants closed entirely due to COVID. The resulting meat shortages and surging prices caused panic in the food supply, and the effects are still being felt two years later.
In the service sector, massive cuts in personnel by airlines were caused when travel bottomed out during the pandemic. Airlines could not afford to keep their schedules intact with many planes flying almost empty. They encouraged pilots nearing retirement to take a buyout and retire early. When air travel surged after restrictions were lifted, the demand quickly created a pilot shortage. (After all, you can’t hire just anybody to be a pilot; it requires years of training and experience.) Again, this shortage continues to disrupt air travel two years later.
The supply chain has been broken.
We are dealing with supply chain problems in the Church as well. In 1 Corinthians 12, we read the Body of Christ is made up of many parts, each serving different functions. The passage emphasizes no body part is more important than another, and the over-arching theme is that we need every part of our body to function properly for the Church to accomplish its mission.
During the pandemic, some church bodies stopped functioning as they should because some parts of the body stopped performing their function. We need everyone to participate fully in the church and perform the duty God has given each individual, or the whole body will suffer. We need to get the church’s supply chain working again to accomplish our mission: reaching the world for Christ.
About the Columnist: David Brown is director of Free Will Baptist Foundation. To learn more about the grants program, visit www.fwbgifts.org.
|
|